I'd arranged with my guide, Ms. Thandar Oo, that I would take a trip around the lake by boat so, at 7.00 a.m., I breakfasted in the capacious restaurant at Villa Inle Resort and Spa and by 8.30 a.m. I'd checked out. Thandar Oo was waiting, this time with one of the elegant 15-metre Inle Boats.
With my luggage on board and sheeted over, we set of along the narrow canal between the hotel and Inle Lake, with the tomato 'fields' on both sides. The 'fields' are actually long and narrow floating strips of organic material laid side-by-side and each pinned to the lakebed with long bamboo poles. We passed local people at work tending the crop.

Around Inle Lake: Tomato growing.
In some places, zucchini were grown, under the same sort of bamboo frames I'd seen during our train journey from Kalaw to Nyaung Shwe.
Once we entered the broad expanse of the Lake, there were numerous Inle boats, similar to our own, noisily heading in all directions. Usually, the motive power is a manual-start, Chinese-made diesel developing 25 horse power costing 500 U.S.dollars new and perhaps 300 U.S. Dollars second-hand. Later in the day I spotted a few Inle boats powered by an automotive engine which was probably more powerful. It was certainly quieter! Some of the smaller boats on the water were of the well-known 'longtail' design and yet others were not motorised at all.
Harvesting Weed
Inle Lake is quite shallow and water weed grows freely. One of the more arduous tasks is collecting water weed from boats, using a long pole to repeatedly lift massive clumps of weed into the boat until it almost sinks. The weed is then dried and used as fertiliser for the tomatoes.

Around Inle Lake: Collecting water weed as fertiliser.
Inle Lake Villages
I was told that there are seventeen distinct villages distributed around the lake, with a total population of around 56,000, plus a further 40,000 people at Nyaung Shwe which serves as the administrative centre of the area.
A broad canal led us to a large village of substantial houses on stilts, raised high above the water. Although some designs recurred frequently, each building reflected the owner's tastes in decor. Some houses were completely made of bamboo but most partially adopted more modern building techniques.

Around Inle Lake: Traditional, bamboo stilt houses.
Piped water (via blue HDPE pipes) and electricity (via a most curious distribution system featuring wooden pylons along all the main canals) were commonplace.

Around Inle Lake: Typical village with its curious electrical distribution system.
The village included a long, open shed housing one of the equally-long man-powered racing boats which compete during the Pagoda Festival. Narrower canals, with a number of footbridges, led us to the rickety wooden landing stage of a family-run silversmith's workshop.
Silversmith's Workshop
Silver ore is reduced to pure metal in a small, clay crucible. This requires a temperature of 800 degrees Celsius produced in a small forge using bellows to supply extra air. The molten silver is cast into a small ingot using a simple mould and, after cooling in cold water, the ingot can be beaten to the required thickness or turned into silver wire using a small 'mangle'. The hard fruit of the Star Anise plant, if warmed for one minute can be grated to give an effective 'soap' for silver cleaning, for clothes washing without fading dyes or as a shampoo. There was a large showroom with an amazing range of silver jewellery. The delicacy of some of the items was astonishing.
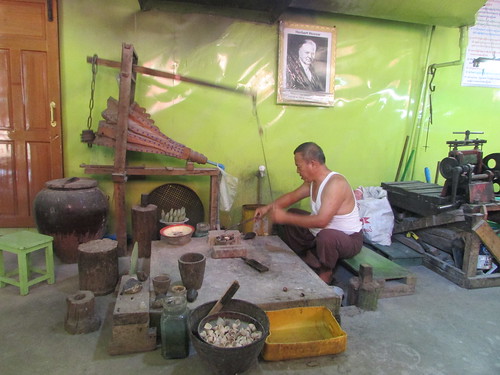
Inle Lake Silversmith: General view of silver smelting workshop.
Boat-building yard
Our next visit was to a boat-building yard. Two 15-metre long hulls of the standard Inle design were virtually complete and I was staggered by the craftsmanship. Only teak wood is used and, when we arrived at the landing stage, two men were starting to turn one two-inch thick teak plank into two one-inch thick planks by sawing. One man stood on a raised sawing platform made of bamboo, one man stood on the ground and between them a massive saw was being worked vertically up and down.

Inle Lake Boat Builder and Cheroot Factory: Sawing a teak plank.
Each of the many frame members required was made from three pieces - left, keel, and right.The keel itself is normally made from three planks to give a slightly convex shape, requiring keel frame members to be curved at the bottom. Keel frame members were being shaped, with considerable accuracy, by another man sitting on the ground merely using an axe.
The structure of the hull had been assembled using wooden dowels, but I didn't identify the wood. Metal woodscrews were used for some features, like attaching the planks forming the top of the gunwhales.
All seams, dowels and screwheads had been caulked using teak sawdust and resin mixed in a simple stone mortar with a pestle to give a dark-coloured paste. Boats built in this traditional way have a long life of tens of years given some maintenance. The purchase cost of 2,500 U.S. Dollars seemed very reasonable to me given the skill and man-hours involved in the construction.

Inle Lake Boat Builder and Cheroot Factory: Completed hull.
Cheroot Factory
Immediately behind the boat-building yatd was a cheroot-making factory. Home-made cheroots can be huge, fat affairs but the commercially-made cheroot is more like the small cigars marketed as 'cigarillo'. Seated on the floor of the factory, a number of women, paid by 'piecework' were deftly assembling the product. According to a sign in English for the benefit of the many tourists around Inle Lake, the ingredients are:-
Cheroot Leaf
Tobacco
Honey
Tamarind
Brown Sugar
Rice Wine
Banana Fruit
Star Anise

Inle Lake Cheroot Factory.
Alodawpauk Pagoda
A boat ride of less than 200 yards took us to one of the landing stages of the important Alodawpauk Pagoda. This was busy with tourists, many apparently from Mynmar. I was told it's an 11th century pagoda which, because of its importance, was restored by the military government in the 1980s. Ongoing development is paid for by private and business donors, some in Thailand.

Alodawpauk Pagoda, Inle: One of the four main Buddha images.
Blacksmith's Factory
After a brief visit to a bamboo handicrafts showroom where modern products for tourists seemed to predominate, we moved on to a blacksmith's workshop. As the boat docked at the usual rickety landing stage, I was sure I recognised it and, indeed, it was the same blacksmith's I'd visited in 2008. That first visit is described in another post called 'Around Lake Inle' which you can find here. Work was being carried on exactly as I'd witnessed the first time, but the personnel had changed.

Inle Lake Blacksmith.
After the blade forging process, sharpening was being carried out by two men, one using a sort of spokeshave to scrape away excess metal, the other using an assortment of metal files to produce the cutting edge. Both men used simple jigs to hold the workpiece but the man with the files also used one foot, like a third hand, to hold the item in the jig.
Impressed with the skills, I determined to purchase a souvenir. I came away with a pair of scissors which I intended to display at home but they proved so sharp they're in daily use in my kitchen.
Lunch
After visiting the blacksmith's workshop, a short boat ride took us to the huge, clean 'Golden Kite Restaurant' built, like the rest of the village, on numerous wooden piles but here the landing stage was, unusually, in good repair. The restaurant was located at the intersection of two major canals so it was rather noisy but we nonetheless enjoyed lunch there.

Return to Nyaung Shwe
Back in our boat, it was time to head back north to Nyaung Shwe. This took about 45 minutes, very pleasant but noisy.

Return to Nyaung Shwe: Speeding north, passing three similar boats heading south.
On arrival at Nyaung Shwe, our driver was waiting to meet us and my luggage was soon transferred to the car. We set of towards Heho for me to catch the afternoon Air KBZ flight back to Yangon. At Shwe Naung, we turned left towards Heho.
Paper making
"We're a little early", Thandar Oo said, telling the driver to stop at a small paper handicrafts workshop up in the hills. We watched two women making sheets of paper from the bark of the Mulberry tree. I'd seen a similar process, but using different plant material, in Bhutan and that's described here. In Myanmar, the mulberry bark is softened with hot water and then pounded with hammers until it becomes a paste which, mixed with water, can be poured onto a muslin-covered wooden frame in a cistern of water. Then, if desired, decoration can be added, creating patterns with leaves and petals before the frame is gently lifted from the water and allowed to drain, leaving a layer of cellulose material which, when dried in the sun, will become paper. A wide selection of products made from this paper were on display.

Nyaung Shwe - Heho: Paper handicraft workshop - decorating the paper with leaves and petals.
Heho Railway Station
We set off again, still early, so I proposed a visit to Heho station. I was able to take a number of photographs and, using Thandar Oo as an interpreter, clarify various technical points with the friendly young stationmaster.
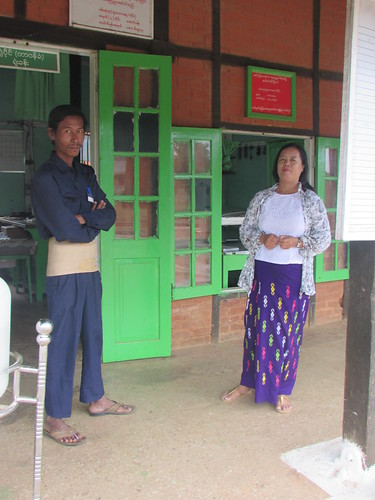
Heho Station: Left - the Stationmaster, right - my Guide Thandar Oo.
Return to Yangon
Heho airport was only a few minutes away and on arrival it was time to say "Goodbye" to my driver and guide. Since it was 'low season', I was surprised at how many tourists were waiting to travel - Japanese, German and various English-speaking travellers. The Air KBZ flight was on time into Yangon where two transfer buses took us to the new Domestic terminal. Doctor Hla Tun was waiting to pick me up, as I was again staying at his home.
Related Posts on this Website
Next Report describing this trip.
All Burma-2017 Trip posts.
My Pictures
Around Inle Lake (2017).
Inle Lake Silversmith.
Inle Lake Boat Builder and Cheroot Factory.
Alodawpauk Pagoda, Inle.
Inle Lake Blacksmith (2017).
Naung Shwe - Heho by road.
Heho Station.
[Links to pictures added 16-Aug-2017: Text amended, pictures added 4-Sep-2017]