When I was driving the 'Planet' replica, people sometimes asked if it was different from driving 'modern' steam locomotives. The answer is "not very, apart from the the fact she's a 'single wheeler', has a rather special braking system and an unusual method of reversing" ('Planet', like its immediate predecessor 'Rocket' has Slip Eccentric reversing). The basic principles of the steam locomotive haven't changed very much since the early days, although the appearance of the 'Planet' replica is very different from modern steam locomotives.
The 'Planet' replica being prepared for service with MOSI volunteer
Bev on the right.
I've already written about driving another early locomotive design in the post Driving 'Lion'. 'Lion' was built just eight years after the original 'Planet' and so there are many similarities, although 'Lion' incorporates Gab motion for reversing.
Adhesion
'Planet' has just one pair of driving wheels, which share the total weight of the locomotive with the leading pair of carrying wheels. Using Whyte's Notation, the arrangement is said to be a '2-2-0'. The total weight on the driving wheels is the 'adhesive weight'. With a single driving axle, not all of the locomotive weight can be adhesive. In the case of the original 'Planet' there was about 5 tons on the driving wheels, with about 3 tons on the carrying wheels. When the driver wants to get the train in motion, steam is used to generate sufficient torque at the driving wheels to move the load. But, if the torque applied to the driven wheels exceeds a critical value (related to the coefficient of friction between the wheels and the rails), the driving wheels slip on the rails and the train does not move.
This was more of a problem with goods trains, which tended to be heavier, so it was desirable to make all the locomotive weight adhesive to reduce the risk of slipping. On goods engines (then called 'luggage engines') the torque generated on the two driving wheels was shared with a similar pair of wheels linked to the driving wheels with coupling rods, giving a wheel arrangement of '0-4-0'. As the size and weight of locomotives increased, further coupled wheels were often used, although 'single-wheelers' weren't eliminated for some years as they could be free-running and, with large driving wheels, fast.
Because the 'Planet' replica only has one pair of driving wheels, it can be 'light on its feet' and prone to slipping so the driver has to take care when starting not to open the regulator too far.
Braking
In the early days of steam locomotives, effort was concentrated on making machines powerful enough to pull a useful load and braking technology was rather neglected. On both the original 'Planet' and the replica, there are two hand brakes, one on each side of the tender, and these are applied by 'screwing down' the handles which project from the top of the tender. Wooden brake blocks are provided which rub against the tyres of the tender wheels to provide braking. On the original 'Planet' that was it! This arrangement wasn't terribly effective in 1830 (severe braking could set the brake blocks on fire!) and, in the replica, the hand brakes are normally used only as a 'parking brake'.
To be acceptable for hauling passenger trains today, the 'Planet' replica also has an Air Brake system. This operates a disc brake on the leading axle of the locomotive, disc brakes on both tender axles and the train brakes. The regulator should always be closed before attempting to brake. I talk a bit about braking and the use of the automatic Vacuum Brake here. Air Brakes form another type of automatic braking (which I've not, to date, described). With the withdrawal of steam traction in the U.K., British Railways started to change over from vacuum braking to air braking and the 'Planet' replica has a version of what became the standard British Railways Two-Pipe Air Braking system.
Converting steam into rotary motion
This part of the locomotive has changed little since the early days. The 'Planet' had two horizontal cylinders at the front between the frames. When the regulator is at least partly open, steam flows through the main steam pipe to feed the two cylinders. The principle is simple - the steam under pressure is used to push a piston to the far end of a steam-tight cylinder. The picture below shows a deliberately 'sectioned' cylinder making the construction clearer. The piston is attached to a Piston Rod which sticks out of one end of the cylinder (through a steam-tight piston gland) and it's the motion of the piston rod which allows the cylinder to do useful work.
As the piston approaches the end of the cylinder, it's necessary to cut off the supply of steam and divert the steam to the other end of the cylinder so as to push the piston back again. This requires a valve in between the steam supply and the cylinder called (logically enough) the Steam Valve. The opening and closing of this valve must be synchronised with the movement of the piston. The two pictures below of the 'Planet' replica give an idea this was engineered in 1830, using complicated iron castings which were at the limit of what was technically possible.
The first picture below is taken inside the smokebox of the 'Planet' replica looking down onto the top of the left hand cylinder with the steam chest removed from the threaded mounting studs so as to show the flat port face area with two rectangular steam ports (connected to each end of the cylinder) and the larger rectangular exhaust port (connected through a passage to the blast pipe).
Top view of cylinder showing the cylinder ports (2 steam, 1 exhaust).
The second picture shows the underside of the steam chest which has been removed in the first picture. The steam chest is complete with the cast rectangular steam valve attached to the valve rod which sticks out of one end of the steam chest (through a steam-tight valve gland). The flat face of the valve bears slides to and fro against the flat port face so this type of valve is called a Slide Valve.
The reciprocating motion of the two piston rods is converted to rotary motion of the driving axle by connecting rods linking the end of the pistons which pull and push a double-crank driving axle, as shown in the picture below. Practical locomotives have at least two cylinders and, on a 2-cylinder design, the cranks are set 90 degrees apart so that both cylinders cannot be on dead centre. This means that a locomotive can always be started (using the effort from at least one cylinder), whatever the position of the cranks.
More than a century after the building of the original 'Planet', similar arrangements remained in use. An increasingly common variation was to move the cylinders outside the frames where the connecting rods drove onto crankpins fitted to the driving wheels, but both inside cylinder and outside cylinder designs lasted until the end of steam. Some designs had additional cylinders and a locomotive might have both inside and outside cylinders. As locomotives became larger, slide valves were replaced by balanced slide valves and then piston valves. A variety of other valves (poppet, sleeve) were tried but piston valves emerged as the most practical form of valve. A few attempts were made using quite different techniques, like steam turbines, but double-acting reciprocating cylinder designs remained virtually unchallenged.Valve Gear
As remarked above, the opening and closing of the steam valve to admit steam from the boiler to either end of the cylinder must be synchronised with the movement of the piston. Since the piston is used to turn the driving axle, if the motion of the steam valve is derived from the turning of the driving axle, the necessary synchronisation is obtained. The motion of the steam valve is derived from the rotation of the driving axle on this design by a special eccentric. A simple eccentric is a type of crank with a small 'throw' - see Wikipedia here. A simple eccentric is fixed to the axle which turns it so as to produce the correct valve events to rotate the driving axle in one direction.
But a locomotive must be able to move in both directions and this was achieved in 'Planet' and other early locomotives by the use of a Slip Eccentric for each cylinder mounted in the middle of the crank axle, as shown in the picture below. A Slip Eccentric is an eccentric which can engage with the crankshaft in two positions where one provides the correct movements of the eccentric rod and the valve rod for clockwise rotation of the driving axle whilst the other position produces anticlockwise rotation of the driving axle. This is achieved by providing lugs or 'dogs' which can engage with one of two mating recesses or pits. A transverse shaft operated from a foot pedal on the footplate is used slide each eccentric across the axle so as to disengage one lug and allow the other lug to engage when the axle has turned so as to bring the other recess in line.
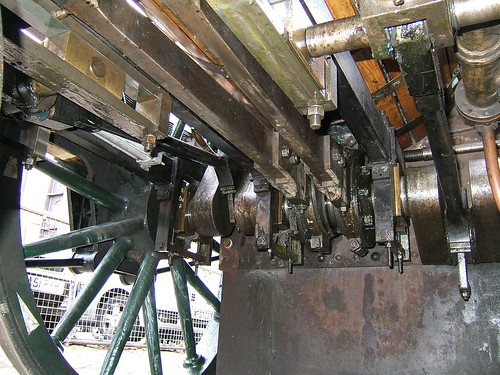
Click here for a larger view
So, reversing the locomotive involves disengaging one lug in the slip eccentrics and turning the driving axle until the other lug engages. Achieving this probably provides the biggest challenge to the driver. There are two ways of achieving this changeover:-
1. Turn the driving axle by controlling the valves manually.Reversing by controlling the valves manually involves operating the foot pedal to the other position, disengaging both valves from the eccentric rods (by operating the two small valve locking levers mounted on top of the left and right footplate railing) and operating the valves appropriately by hand (using the two curved levers mounted on the boiler backhead facing the driver) so as to move the locomotive. When the eccentrics have re-engaged, the two small valve locking levers are used to re-connect the eccentric rods with the valves, allowing the locomotive to be driven normally.
2. Perform a 'flying reverse'.
The 'flying reverse' is potentially simpler but requires careful judgment. This can be used if the locomotive is already in motion in one direction and requires to stop and then re-start in the opposite direction. The driver closes the regulator and uses the brakes so as to stop in the correct position. Before actually stopping, the foot pedal is operated to the other position. If judged correctly, the slip eccentrics will engage for the opposite direction before the locomotive comes to a stand. The 'flying reverse' can also be used if the locomotive is stationary but on a sufficient gradient so that it will roll when the brakes are released.
The view below of the footplate of the 'Planet' replica, shows the location of the controls used by the driver when reversing.
The 'Planet' replica in the Power Hall at MOSI. L-R: Steam chest pressure gauge, valve locking lever (on top of railing), two long curved levers (for manual operation of valves), foot pedal (for reversing), water gauge, regulator, water gauge, blower valve with injector steam cock below, boiler pressure gauge, valve locking lever (on top of railing).
Click here for a larger view
The two valve locking levers and the two long curved levers for the manual operation of the valves connect to the front of the locomotive via a series of rods. The picture below shows the two rocking shafts (top of picture) which operate the valve spindles controlling the valves in the steam chests described above. When the small valve locking levers are engaged, each rocking shaft is driven by the associated eccentric rod. To allow manual operation of the valves, the small valve locking levers disengage the eccentric rods from the rocking shafts by two shafts operating lifting links (near the bottom of the picture, painted green) which disengage each eccentric rod from its valve spindle.
Click here for a larger view
Development of Valve Gear
Slip eccentric reversing of locomotives did not survive. By providing four fixed eccentrics and eccentric rods, rather than two, the correct valve movements for both directions of movements on two cylinders could be provided. Initially, a mechanism connected to a simple reversing lever on the footplate connected two of the four eccentric rods to the valve spindles. For instance, 'Lion' of 1838 features Gab motion.
But, by 1842, Stephenson's link motion appeared in the U.K. offering not only reversing but variable cut-off allowing steam to be used expansively for greater efficiency. This became the predominant valve gear in the U.K. for many years. Don Ashton's authoritative review of Stephenson Link Motion can be found here,
For comparison with the picture above showing "Planet's" driving axle and eccentrics, the picture below shows "Sapper's" driving axle and eccentrics. "Sapper" is an 0-6-0 'Austerity' tank built more than a century after the original "Planet". Stephenson Link Motion had replaced slip eccentric reversing but otherwise the layout is similar.
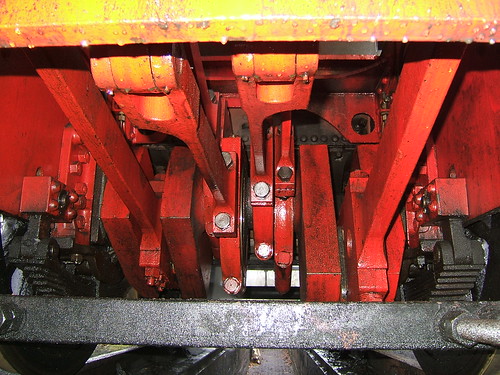
Click here for a larger view
Design issues
In general, materials and manufacturing techniques now are far superior to anything available in 1830. Steel was not available then - wrought iron was the best material but quality was very variable and only limited size sheets were available which required joining by riveting. Cast iron in the complex forms required for cylinders and valve chests was pushing at the limits of the technology available at the time.
The 'Planet' replica incorporates a number of features which were not possible in 1830 (for instance, air brakes, blower, injector, whistle, water gauges, pressure gauges) but that discussion I'll defer to a later article.
Related posts on this website
Early Locomotive Design.
The Planet Replica.
If your interest is broader than just the 'Planet' replica, there's a series of articles describing working on preserved railways and driving various steam locomotives. Most of these articles can be found here
My Pictures of the 'Planet' replica
'Planet'.